Producing 3D Printed N95s
VMASC faculty, Dr. Barry Ezell and Hector Garcia, have facilitated a distributed 3D printing network to aid Hampton Roads' current personal protective equipment shortage. In collaboration with the Computational Modeling and Simulation Engineering Department, the face masks were tested and approved by CHKD. VMASC continues to produce 40 masks on a weekly basis, alongside an additional 20 masks a week from the Brooks Crossing Innovation Lab.
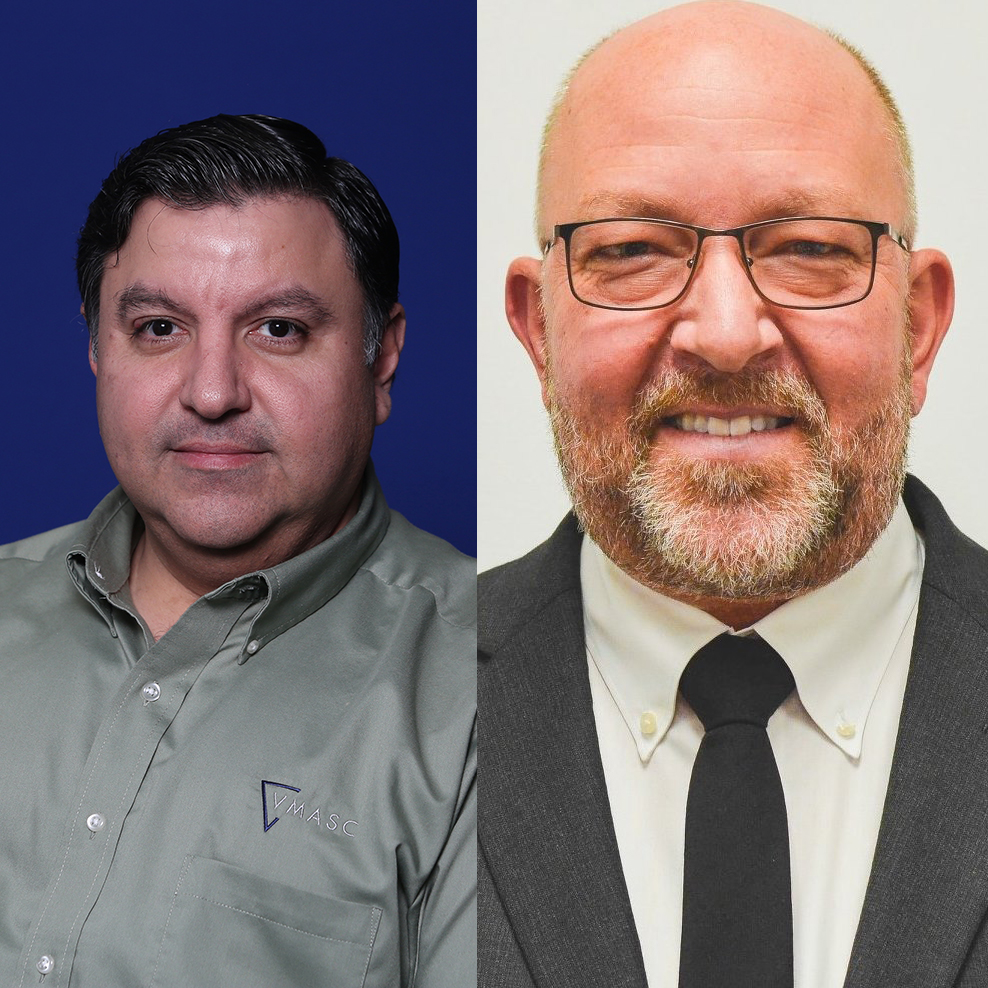
ABOUT THE PROJECT—
The Virginia Modeling, Analysis, and Simulation Center (VMASC) is utilizing their expertise in additive manufacturing and laser cutting to aid Hampton Roads current personal protective equipment shortage. At this time, VMASC is facilitating a distributed 3D printing network to mass-produce the much-needed face masks. The open-source 3D printed face mask is coated with acrylic to eliminate seal the 3D printing material, PLA, and foam is added to the back of the mask for comfort. Lastly, the masks' air filter attachments are cut through VMASC's laser cutting technologies and snapped onto the mask. The newest collaboration partner, the Frank Reidy Research Center for Bioelectrics, will help enhance the masks’ filtering abilities using advanced electro spinning processing.
In collaboration with Computational Modeling & Simulation Engineering Department, the face masks have been tested and approved by the Children's Hospital of The King's Daughters (CHKD) infectious disease laboratory and can be sanitized through the use of clinical bleach or antibacterial wipes.
After establishing existing relationships in the healthcare industry and receiving certification of the 3D printed face mask, VMASC’s Deputy Executive Director Dr. Barry Ezell went to the Virginia Department of Emergency Management (VDEM) and the Virginia Secretary of Education’s office with the idea of crowdsourcing the 3D-printed N95 masks across the state. The Virginia Secretary of Education’s office loved the innovative idea and in collaboration with VMASC and VDEM, they’re collecting data for what and where the capabilities to fabricate, assemble, and certify the masks are across the Commonwealth to direct the activities. Public and private colleges and universities in Virginia are being targeted to replicate the process.
VMASC will continue to produce 40 face masks on a weekly basis and the Brooks Crossing Lab will assist with an additional 20 face masks per week. The masks are scheduled to be delivered on a weekly basis to CHKD and other interested healthcare partners.
Producing 3D Printed N95s
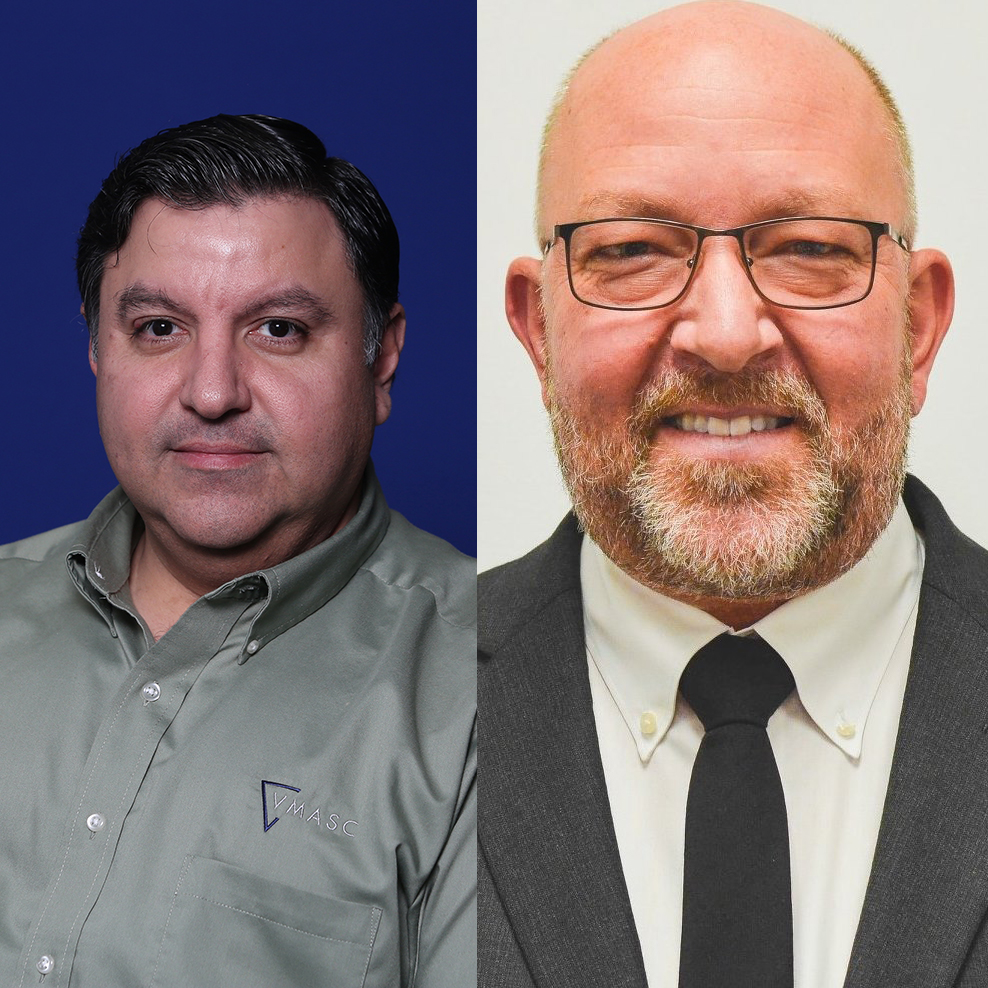
PRODUCING 3D PRINTED N95S
The Virginia Modeling, Analysis, and Simulation Center (VMASC) is utilizing their expertise in additive manufacturing and laser cutting to aid Hampton Roads current personal protective equipment shortage. At this time, VMASC is facilitating a distributed 3D printing network to mass-produce the much-needed face masks. The open-source 3D printed face mask is coated with acrylic to eliminate seal the 3D printing material, PLA, and foam is added to the back of the mask for comfort. Lastly, the masks' air filter attachments are cut through VMASC's laser cutting technologies and snapped onto the mask. The newest collaboration partner, the Frank Reidy Research Center for Bioelectrics, will help enhance the masks’ filtering abilities using advanced electro spinning processing.
In collaboration with Computational Modeling & Simulation Engineering Department, the face masks have been tested and approved by the Children's Hospital of The King's Daughters (CHKD) infectious disease laboratory and can be sanitized through the use of clinical bleach or antibacterial wipes.
After establishing existing relationships in the healthcare industry and receiving certification of the 3D printed face mask, VMASC’s Deputy Executive Director Dr. Barry Ezell went to the Virginia Department of Emergency Management (VDEM) and the Virginia Secretary of Education’s office with the idea of crowdsourcing the 3D-printed N95 masks across the state. The Virginia Secretary of Education’s office loved the innovative idea and in collaboration with VMASC and VDEM, they’re collecting data for what and where the capabilities to fabricate, assemble, and certify the masks are across the Commonwealth to direct the activities. Public and private colleges and universities in Virginia are being targeted to replicate the process.
VMASC will continue to produce 40 face masks on a weekly basis and the Brooks Crossing Lab will assist with an additional 20 face masks per week. The masks are scheduled to be delivered on a weekly basis to CHKD and other interested healthcare partners.
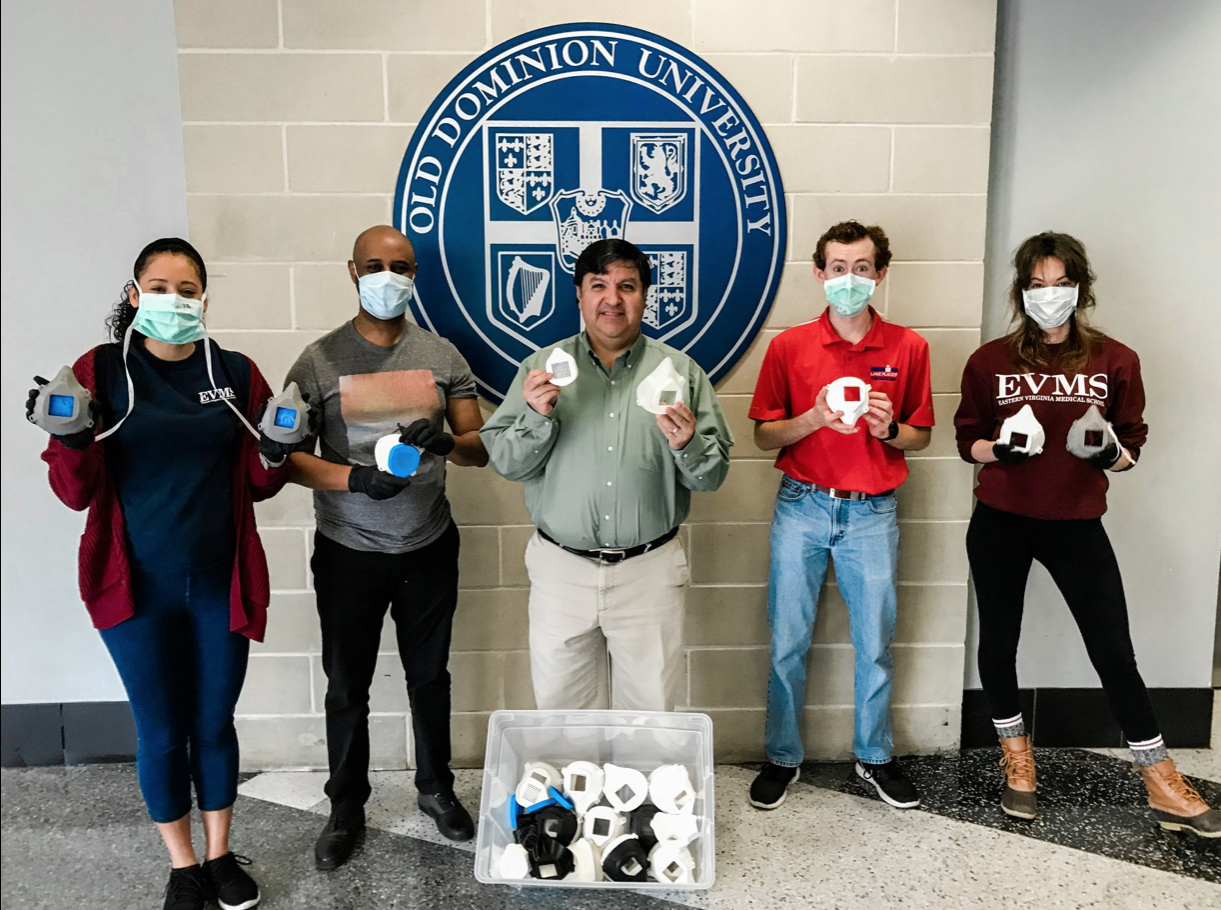
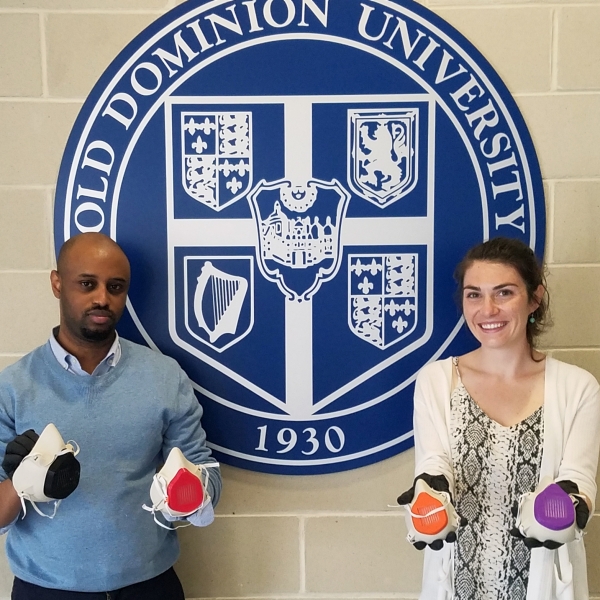
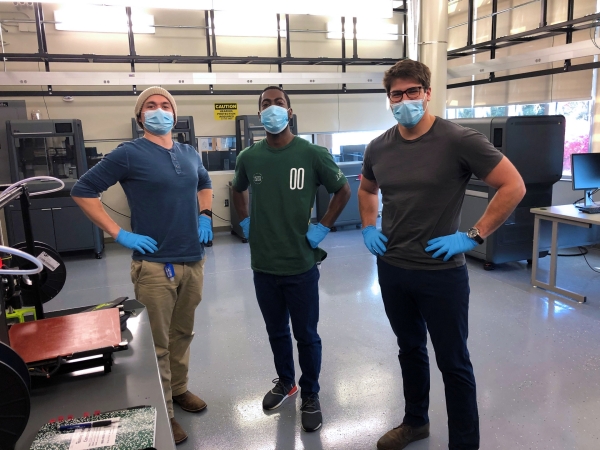
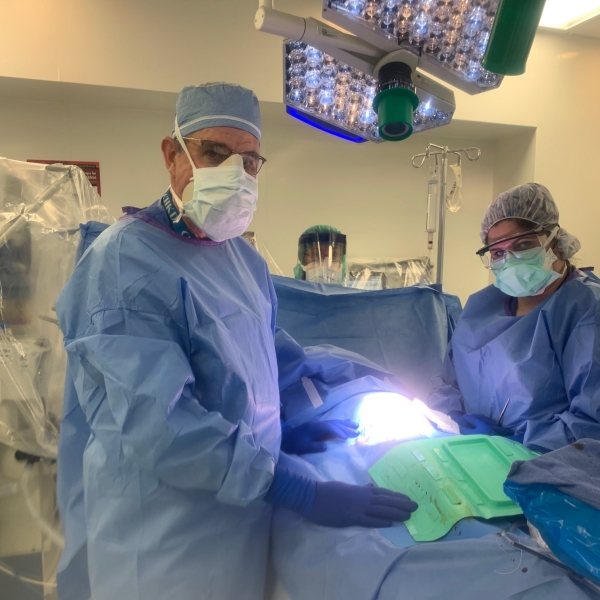
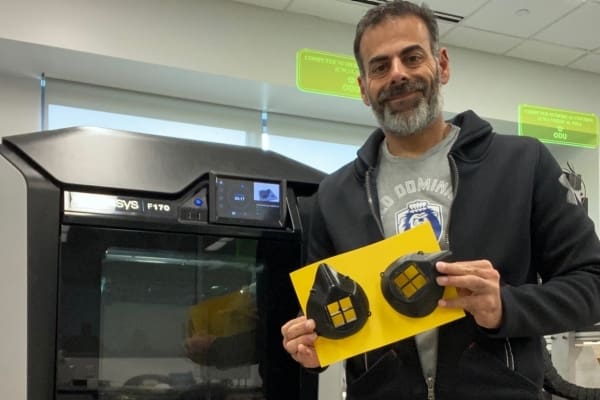